
Rather than doing the job correctly the first time, the test-oriented culture aims to get the development done right the second time - a wasteful mindset.
Toyota production system software#
In effect, they expect the software code to fail and for automated testing to capture the failure and then create a bug or incident requiring rework. Most software engineering teams clash with this point, as one of the latest methodologies is test-driven design. However, essential capacity management solutions, story points, and work-in-process limits can likely get you 80% of the way before diving into a full-fledged Enterprise Resource Planning (ERP) solution. Far easier to achieve in theory than reality. They sought an optimal flow where no single person or team is either overloaded or left twiddling their thumbs. Level out the workload ( Heijunka), briefly is capacity utilization and workload leveling. Responsiveness to day-to-day or even hourly demand is the goal, versus a Scrum solution that focuses on a set period. Pull system or Kanban allows the production (development) team to select the next highest priority or most valuable action from a ranked backlog. Use pull systems to avoid overproduction.
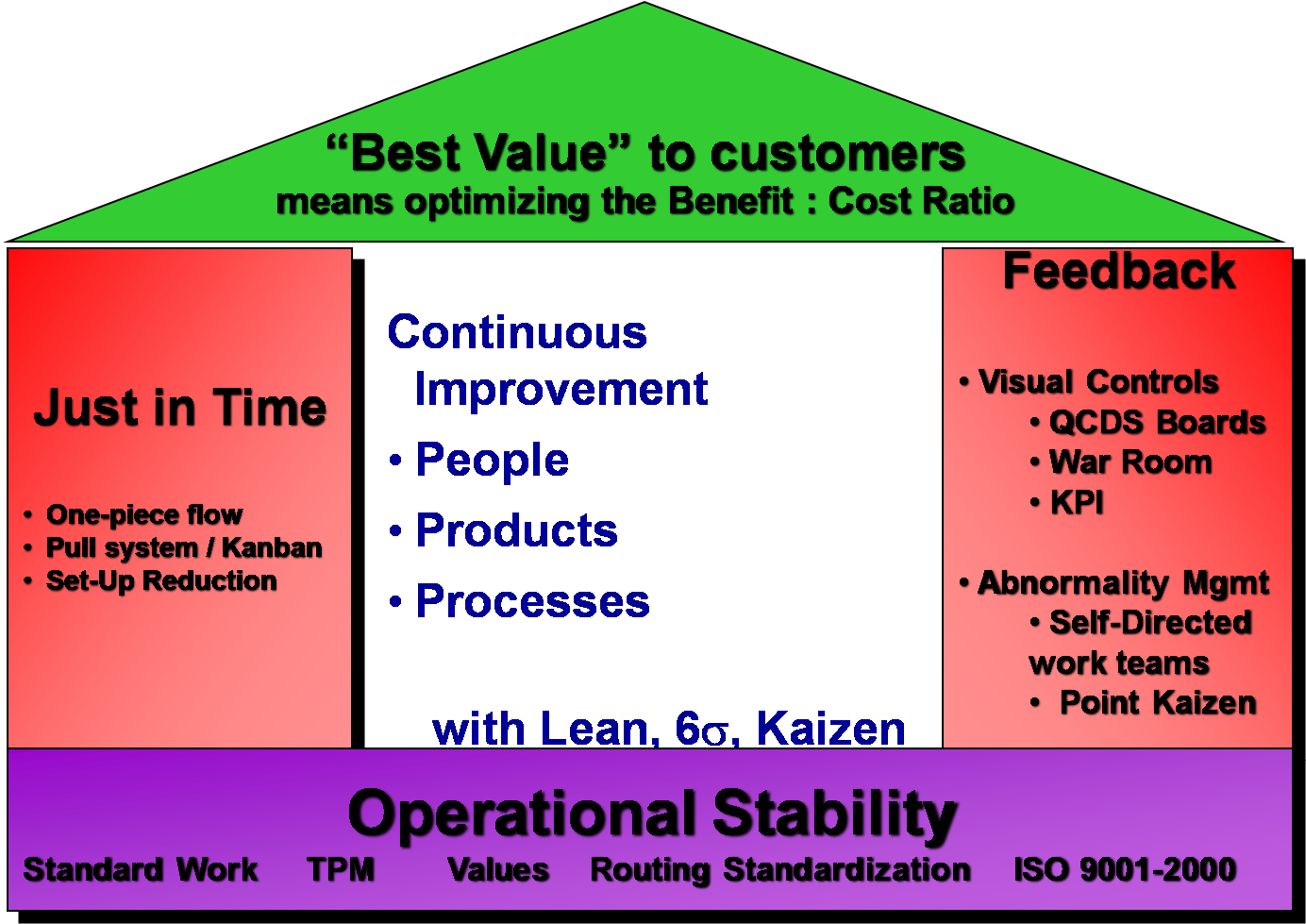
Minimize Work in Progress (WIP) with a Just in Time (JIT) production logistics chain. Provide downline customers with what they want, how they want it when they want it. Surface problems immediately and solve them quickly. Pursue high-value-added work first in a continuous flow. Use continuous process flow to surface problems. The right process will produce the right results. The TPS is designed for the long-term, years or decades, not the short-term quarterly outlook that has permeated so much of American business, never looking beyond the next few quarters while their International competitors are looking 25 years down the road. Genchi Genbutsu - “going to the source.” In short, the art of walking around, followed by the Five Whys while talking with the subject matter experts (SME). In contrast, many Japanese companies are aiming for constant small improvements, improving the process over time. This is the one area where the mindsets clash, as most American companies are fond of moon shot efforts, giant leaps in technology and capabilities. For a company to coalesce around its vision, sometimes you have to stare at the horizon, leave your comfort zone and just go for it. Go to Mars in 2024, build 500,000 Tesla Cars a year. One has to look no further than SpaceX or Tesla to see Big Hairy Audacious Goals ( BHAG) in action. Each team member is expected to do their best, improve their competency, and be held accountable for their actions towards achieving results while growing in both responsibilities and core competencies. This ideally builds on trust and understanding, leading to a diverse set of opinions.Įncourage your workforce to be part of a team and not a solo achiever. Respect for individuals’ right to express themselves via culture, beliefs, identity, and who they are as a person.
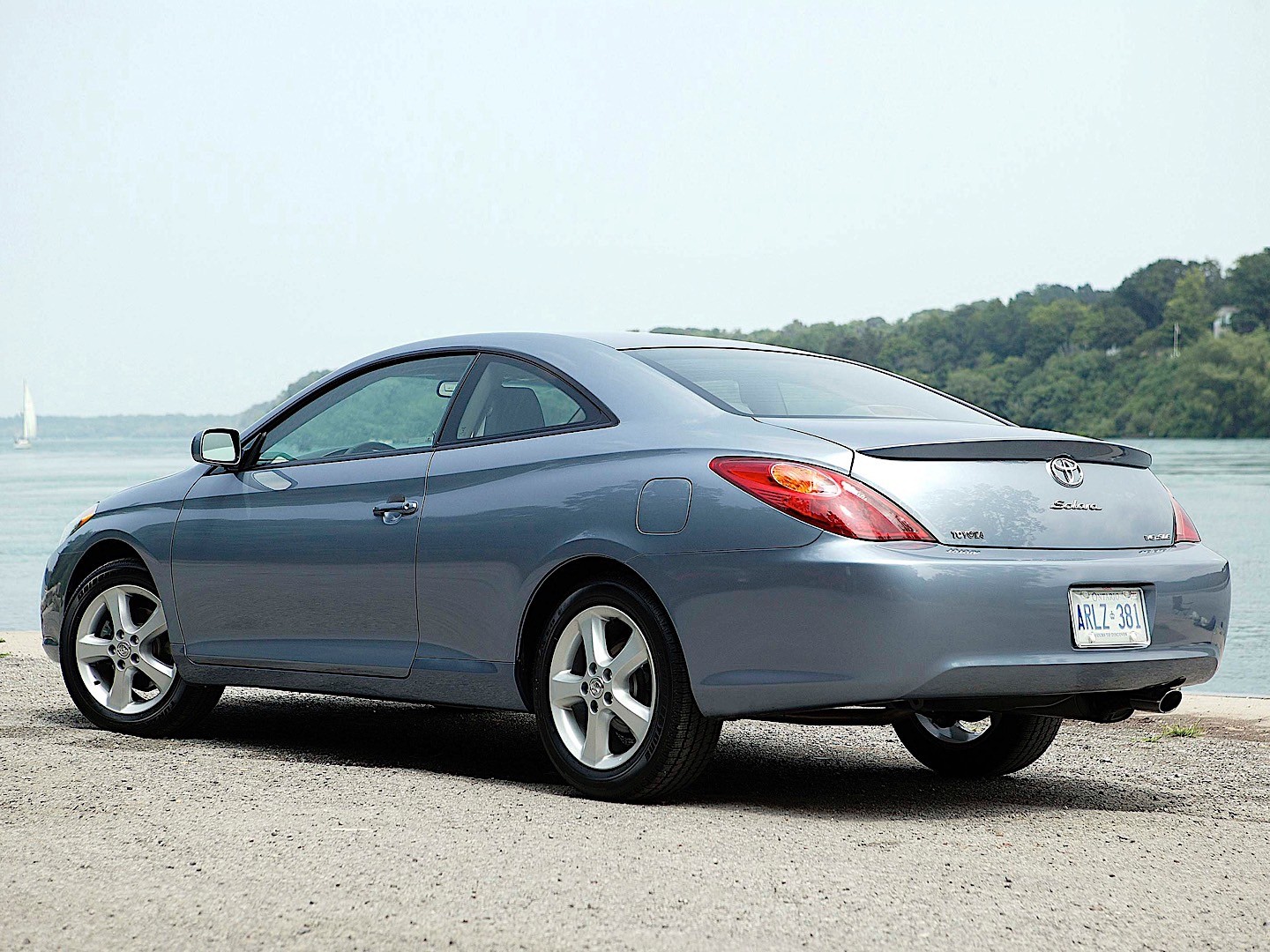
It is the foundation of our corporate culture.” - Toyota EU, 2021.
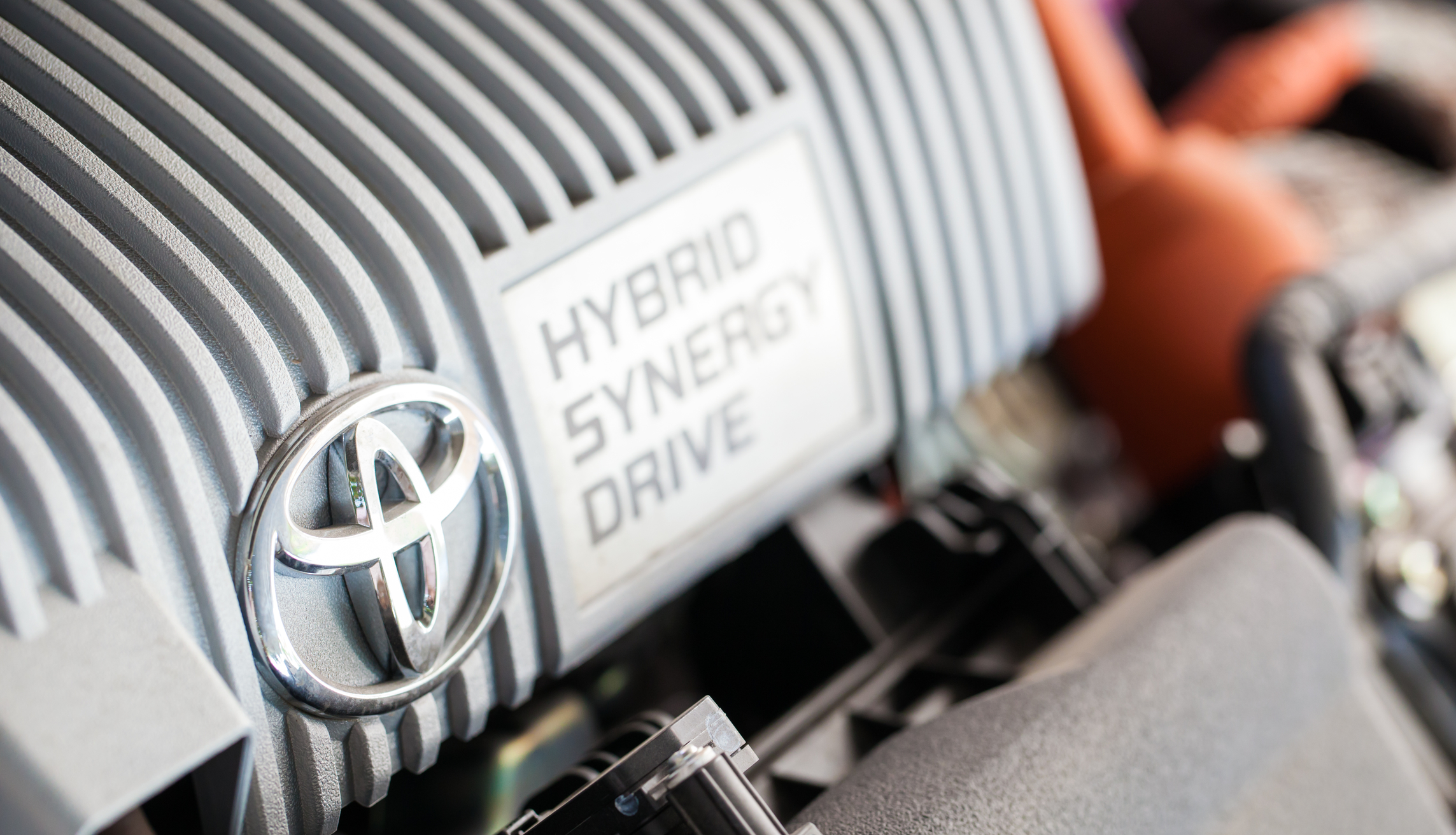
“The Toyota Way defines the fundamental values and business methods all our people should apply in every aspect of their day-to-day work, at every level of the company, worldwide. All principles and methodologies that follow are based upon these two pillars. There are two pillars behind the Toyota Way, Continuous Improvement and Respect for people. The primary goal of TPS is to eliminate waste in all of its guises.
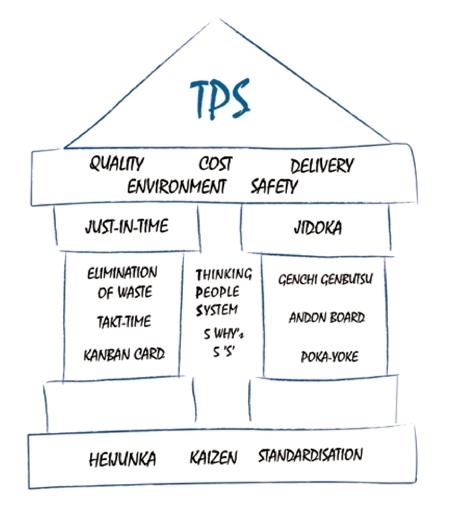
The part was reordered and delivered just in time before the production line was forced to stop. This inventory process became the basis of the Toyota Production System - nearly one days’ worth of inventory. From Piggly Wiggly’s perspective, when they hit a part inventory shortage, they simply ordered more, never carrying more than required. In America, you could take a shopping cart, get precisely what you wanted, when you wanted it, and be done, a highly efficient system. Japan had no equivalent at the time, where shop keepers assembled your order behind the counter. On the visit, Taiichi also visited an American Grocery store, Piggy Wiggly. While Taiichi was suitably impressed with the operations, there was no way that Toyota could match the gigantic capital outlays for months of inventory and sprawling operations at this scale. In 1953 Taiichi Ohno (the father of the Toyota Production System) visited Michigan, and Ford’s massive River Rouge production facility was the largest in the world. Taichii Ohno, the father of Toyota Production System
